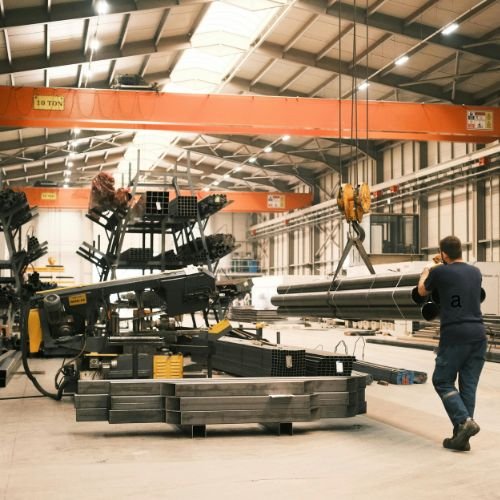
Industrial machinery can work smoothly for a long period of time, but all it takes is one equipment malfunction to instantly turn efficiency into chaos, creating potential safety risks in the process. According to statistics, industrial equipment malfunctions account for a significant portion of workplace injuries. In 2023 alone, there were 779 deaths and 780,690 DART cases attributed to causes like contact with objects and equipment, collapse or engulfment, and struck-by accidents. These numbers represent preventable tragedies, and in this article, we’ll explore methods of prevention.
Safe Design
When you build systems from the start with safety in mind, they’re less likely to malfunction unexpectedly. Using elements like automatic shutdowns and fail-save valves can protect against faults. Additionally, certified systems that automatically prevent hazardous events when limits are exceeded are typically mandated in certain industries, like chemical and petrochemical plants.
One of the most devastating breakdowns is overheating, and it can cause a cascade of problems. Industrial machinery is particularly prone to overheating due to its size and the demand for constant usage. High temperatures degrade bearings, warp metal, and fry electronics. However, a well-maintained chiller system can prevent heat stress that leads to cracking and combustion. If any of your systems don’t include temperature regulation, you’re risking catastrophic damage and injury. Smart engineering from the start can help prevent future disasters.
Regular Maintenance and Inspections
The importance of regular maintenance and inspections can’t be overstated. One faulty component can have devastating consequences. For example, in 1990, an explosion at the ARCO Chemical Channelview plant killed 17 workers and injured five after a faulty oxygen analyzer caused an ignition. This failure was entirely preventable and resulted in a $3.4 million fine. Unfortunately, these accidents aren’t rare. Broken equipment causes thousands of incidents each year because companies aren’t prioritizing safety.
It’s crucial to prioritize scheduled preventive maintenance that includes regular inspections to catch malfunctioning components before they lead to disaster. For instance, thermal cameras and vibration sensors can catch motor imbalances and overheating before it becomes an issue, and IoT sensors can provide ongoing data to an AI system to identify potential failures. By implementing regular maintenance and performing inspections, you can maintain a higher level of safety and reduce downtime.
Machine Guards
Unshielded machinery parts can become as dangerous as bullets and shrapnel when workers can get close to running machinery. Bypassing critical lockout mechanisms often leads to fatalities. Installing hardened shields and interlock systems is essential for preventing access while machines are running. But it’s not enough to install lockouts. You also need to train workers and make them aware of the lockout systems and explain why they should never try to bypass them for any reason. This leads into the next point.
Thorough, ongoing Training
No matter how many safety features you install, you still need to thoroughly train your workers to manage it all. Training eliminates a large number of hazards. Workers need to know what issues to look out for and report. For example, frayed hoses, strange noises, and warm bearings are all potential failures waiting to happen. Teams also need a structured system for reporting hazards and near misses. However, many workers ignore issues because they haven’t been taken seriously in the past. But when a company empowers workers to pause operations if they sense danger, things change. In fact, many companies report a significant decrease in incidents after implementing Stop Work Authority (SWA).
Emergency Response Planning
Sometimes an incident can be contained before it becomes a crisis, but this requires a strong emergency response plan. Emergency shutdown procedures along with spill, fire, and explosion protocols are essential. Most importantly, all industrial operations need on-site first-aid and planned evacuation routes. Many catastrophic disasters start small, but your response protocol can prevent an all out crisis.
Safety is a System
Preventing catastrophic machinery failures isn’t just a matter of checking off maintenance tasks and calling it a day. It requires a layered approach where every part of your operation works in harmony to reduce risk. Maintaining, inspecting, and monitoring equipment is just one component. Regulating heat, shielding machinery, and empowering employees to act responsibly without fear of reprimand are equally necessary for prevention.
It’s not a matter of “if” a failure will occur. It’s a matter of “when,” and how it plays out will depend on the strength of your prevention and response strategies. Not all incidents can be prevented, but a strong safety system can reduce the frequency of accidents and save lives.